20L oil filling machine liquid production line
20L Oil Filling Machine Liquid Production Line is a complete system designed to automate the process of filling 20-liter containers (drums, pails, or jerrycans) with oil or other liquid products. This production line integrates various machines and processes to ensure efficient, accurate, and safe filling, capping, labeling, and packaging. It is widely used in industries such as lubricants, edible oils, chemicals, and biofuels.
Components of a 20L Oil Filling Machine Liquid Production Line:
Unscrambler or Container Loading System:
Automatically feeds empty containers (drums, pails, or jerrycans) into the production line.
Ensures proper orientation and positioning for filling.
Filling Machine:
Type: Gravity filler, piston filler, pump filler, or net weight filler.
Function: Accurately fills 20L containers with oil or other liquids.
Accuracy: ±0.1% to ±0.5% of target volume or weight.
Speed: 10–60 containers per hour, depending on the system.
Capping Machine:
Automatically applies caps or lids to filled containers.
Types: Screw cappers, snap cappers, or press cappers, depending on the container type.
Labeling Machine:
Applies labels to filled and capped containers.
Can handle pre-printed or blank labels with variable data (e.g., batch numbers, expiration dates).
Conveyor System:
Transports containers between different stages of the production line.
Types: Belt conveyors, roller conveyors, or chain conveyors.
Inspection Systems:
Checkweigher: Ensures each container meets the required weight specifications.
Leak Detector: Checks for leaks in sealed containers.
Vision System: Inspects labels, caps, and fill levels for quality control.
Packaging and Palletizing:
Control System:
Advantages of a 20L Oil Filling Machine Liquid Production Line:
High Efficiency: Automates the entire process, reducing manual labor and increasing throughput.
Accuracy: Ensures consistent filling, capping, and labeling, minimizing product waste.
Scalability: Can be customized to handle different container sizes, oil types, and production volumes.
Safety: Reduces operator exposure to hazardous materials and minimizes spillage.
Traceability: Integrated inspection and labeling systems ensure product quality and compliance with industry standards.
Applications:
Edible Oils: Filling 20L containers with cooking oils, such as sunflower oil, olive oil, or soybean oil.
Lubricants: Dispensing motor oils, gear oils, or hydraulic fluids.
Chemicals: Handling solvents, acids, or cleaning agents.
Biofuels: Filling containers with biodiesel or other renewable fuels.
Industrial Oils: Packaging transformer oil, cutting oil, or heat transfer fluids.
Types of Filling Machines Used in the Production Line:
Gravity Fillers:
Piston Fillers:
Pump Fillers:
Net Weight Fillers:
Considerations When Designing a Production Line:
Oil Properties:
Production Volume:
Container Type:
Automation Level:
Safety and Compliance:
Example Specifications for a 20L Oil Filling Machine Liquid Production Line:
Filling Capacity: 20 liters per container.
Filling Speed: 10–60 containers per hour.
Accuracy: ±0.2% of target volume or weight.
Power Supply: 220V/380V, 50Hz/60Hz.
Material: Stainless steel (SS304 or SS316) for food-grade applications.
Workflow of a 20L Oil Filling Machine Liquid Production Line:
Container Loading: Empty containers are fed into the line using an unscrambler or conveyor.
Filling: Containers are filled with oil using the filling machine.
Capping: Filled containers are sealed with caps or lids.
Labeling: Labels are applied to the containers.
Inspection: Containers are checked for weight, leaks, and label accuracy.
Packaging: Filled and labeled containers are packed into boxes or crates.
Palletizing: Packed containers are stacked onto pallets for storage or shipment.
A 20L Oil Filling Machine Liquid Production Line is a comprehensive solution for businesses looking to automate their oil packaging process. It improves efficiency, accuracy, and safety while ensuring consistent product quality. Whether you're handling edible oils, lubricants, or chemicals, this production line can be customized to meet your specific needs.
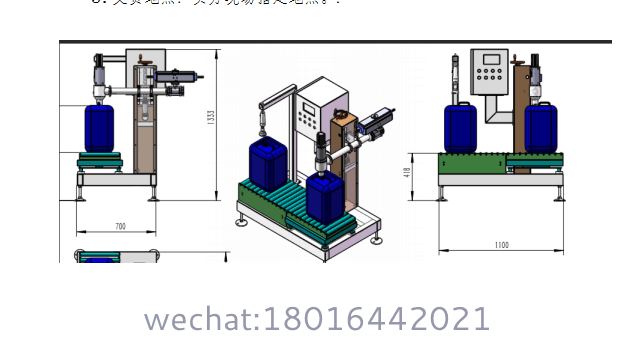