Semi-Automatic Drum Filling System
Semi-Automatic Drum Filling System is a type of equipment designed to fill drums or containers with liquids, powders, or granular materials with a combination of manual and automated processes. It is commonly used in industries such as chemicals, food and beverage, pharmaceuticals, and oil and gas, where precise and efficient filling of drums is required.
Key Features of a Semi-Automatic Drum Filling System:
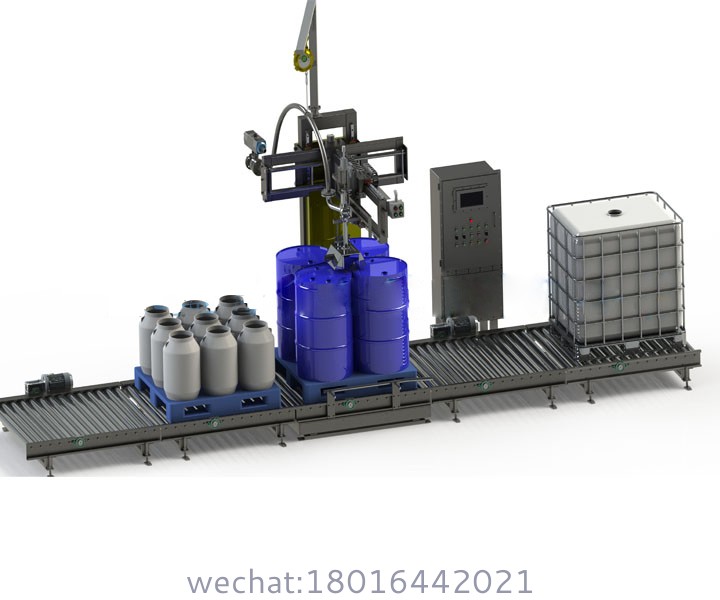
Automated Filling Mechanism:
Uses pumps, flow meters, or load cells to measure and control the amount of material being dispensed into the drum.
Ensures accurate and consistent filling, reducing waste and improving efficiency.
Manual Drum Handling:
Control Panel:
A user-friendly interface (e.g., touchscreen or buttons) allows operators to set filling parameters such as volume, weight, or time.
The system can be programmed for different drum sizes and materials.
Safety Features:
Includes spill containment, overfill protection, and emergency stop functions.
May have grounding systems to prevent static discharge when handling flammable liquids.
Material Compatibility:
Designed to handle a wide range of materials, including corrosive, viscous, or hazardous substances.
Constructed from materials like stainless steel for durability and resistance to corrosion.
Flexibility:
Can be adapted to fill different types of drums (e.g., open-top, tight-head) and container sizes.
Suitable for both liquid and dry products.
Advantages of a Semi-Automatic Drum Filling System:
Cost-Effective: More affordable than fully automatic systems, making it ideal for small to medium-sized operations.
Improved Accuracy: Reduces human error in measuring and filling.
Increased Productivity: Faster than manual filling, while still allowing operator oversight.
Scalability: Can be upgraded to a fully automatic system as production needs grow.
Applications:
Chemical Industry: Filling drums with solvents, acids, or adhesives.
Food and Beverage: Dispensing oils, syrups, or other liquid ingredients.
Pharmaceuticals: Handling sensitive or hazardous materials with precision.
Paints and Coatings: Filling drums with paints, resins, or coatings.
Considerations When Choosing a System:
Material Properties: Ensure the system is compatible with the viscosity, density, and corrosiveness of the material.
Drum Size and Type: Verify the system can accommodate the specific drums used in your facility.
Throughput Requirements: Choose a system that meets your production volume needs.
Safety and Compliance: Ensure the system meets industry standards for handling hazardous materials.
A semi-automatic drum filling system strikes a balance between manual and fully automated systems, offering efficiency and precision while maintaining flexibility and cost-effectiveness. It is an excellent choice for businesses looking to optimize their drum-filling processes without investing in a fully automated solution.