Chemical Solvent Liquid Filling Machine - 200L Liquid Filling Machine - Swing Arm Liquid Filling Machine
Chemical Solvent Liquid Filling Machine - 200L Liquid Filling Machine - Swing Arm Liquid Filling Machine
Our Company Specializes In:
A comprehensive range of packaging equipment, including:
Fully automatic weighing liquid filling machines
Semi-automatic liquid filling machines
Automatic capping and screwing machines
Automatic lid feeding machines
Labeling conveyors and wrapping machines
Fully automatic packaging machines and palletizing production lines
Palletizers and other complete filling/packaging solutions
Technical Parameters:
Parameter | Details |
---|---|
Filling Range | 60-200kg |
Filling Speed | 4-5 tons/hour (requires sufficient pipe diameter & good liquid flow) |
Weighing Platform | 800×760mm |
Suitable Barrel Height | ≤1000mm (customizable for varying heights) |
Applicable Barrel Neck | ≥40mm (filling caliber adapts to barrel opening) |
Division Value | 0.01kg |
Filling Accuracy | 1-3‰FS |
Compressed Air | 0.3-0.6MPa |
Operating Environment | Temperature: -10°C to +45°C, Relative Humidity ≤90% |
Power Supply | AC220V, 50Hz, 0.3Kw |
Note | Material viscosity <20000cp; pre-filling pressure: 0.3±0.1MPa; flow >300L/Min |
Key Features:
Manual/Automatic Mode: Flexible operation switching.
Precision Weighing: Uses imported components for accuracy.
Quick Parameter Setup: Intuitive shortcut keys for fast adjustments.
Multi-Recipe Storage: Stores up to 10 formula configurations.
Dual-Speed Filling: Adjustable fast/slow feeding rates.
Anti-Collision Design: Automatically retracts filling gun on impact.
Self-Correcting System: Enhances accuracy for subsequent fills.
Smooth Operation: Linear guide rails ensure effortless movement.
Vibration Damping: Locking mechanism minimizes errors from motion.
Diagnostic Alarms: Weighing errors and faults trigger instant alerts.
Automatic Taring: Compensates for variable container weights.
Corrosion Resistance: 316 stainless steel for material contact; PTFE plug for harsh chemicals.
Production Tracking: Counts filled barrels and total weight automatically.
Explosion-Proof Option: Suitable for hazardous environments (customizable).
Automated Capping: Optional add-on for streamlined workflows.
Heating System: Optional insulation for temperature-sensitive materials.
Data Connectivity: Standard RS232/485 ports; optional industrial bus protocols.
Equipment Workflow:
Automatic decapping
Barrel cleaning and rinsing
Barrel feeding and positioning
Sterilization and flushing
Precision filling
Lid alignment, capping, and pressing
Quality inspection (lamp check)
Heat-shrink film sealing
Final bagging and conveying
Applications:
Industries: Food processing, pharmaceuticals, chemicals.
Materials: Liquids, solvents, oils, and low-viscosity chemicals.
After-Sales Service:
Service Booking: Schedule via hotline for prompt assistance.
On-Site Support: Engineers dispatched within 24 hours for debugging/maintenance.
Comprehensive Repairs: Swift resolution of equipment issues.
Post-Repair Inspection: Thorough testing and hidden-problem checks.
Transparent Reporting: Detailed maintenance records and pricing.
Follow-Up: Callback within 3 working days post-service.
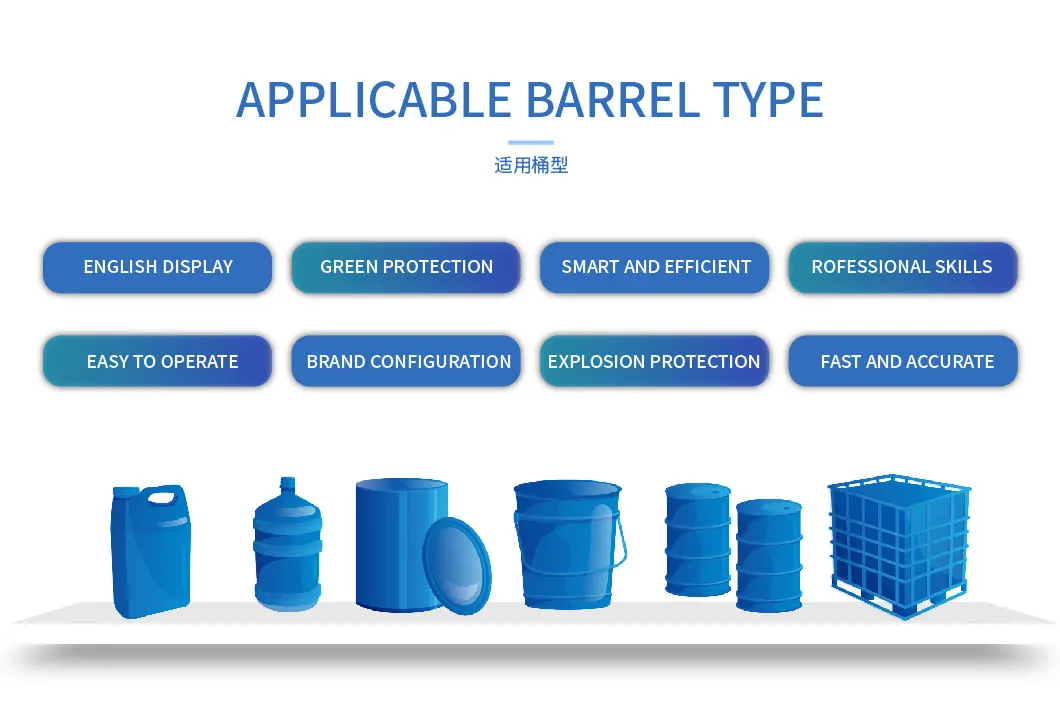
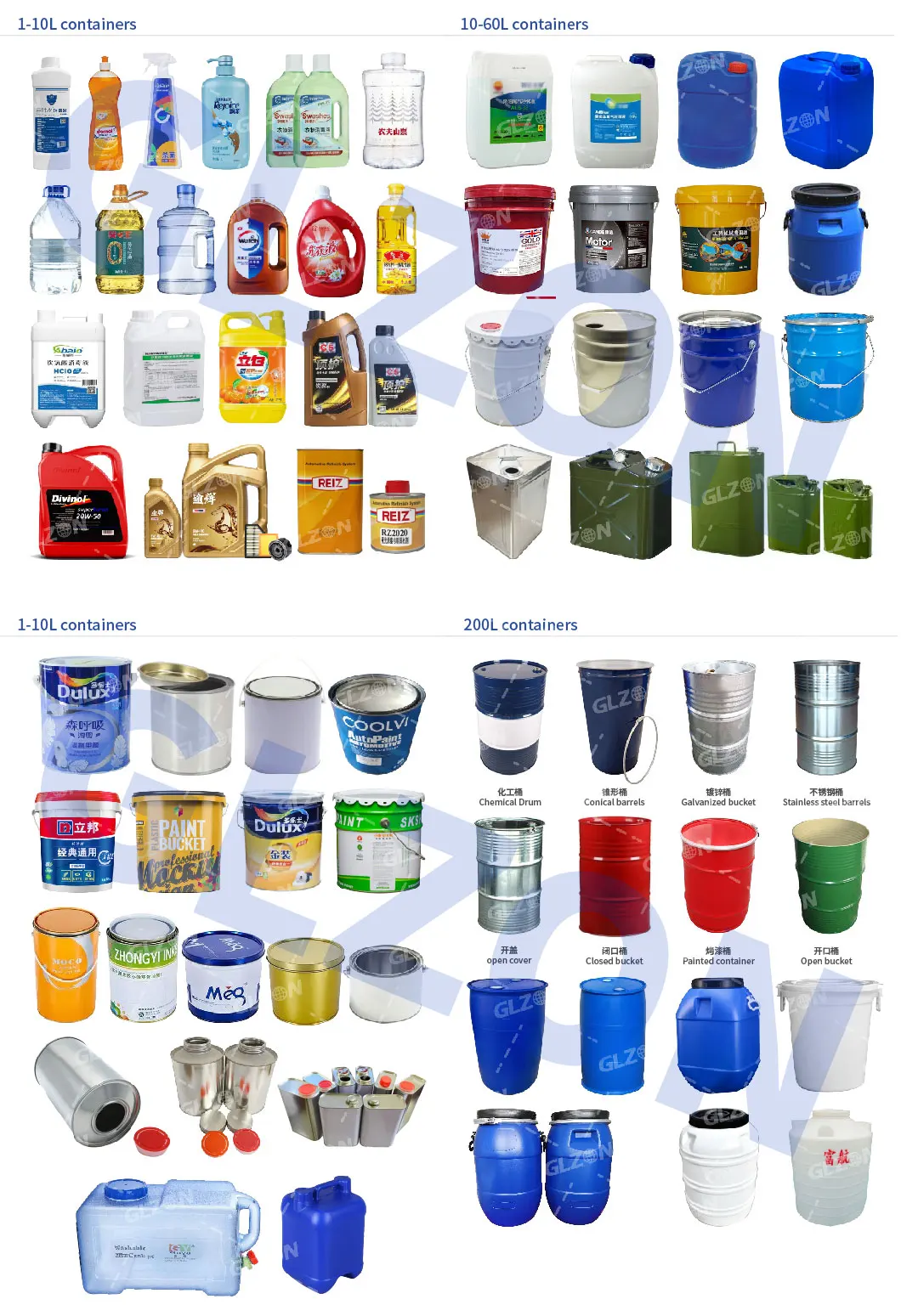
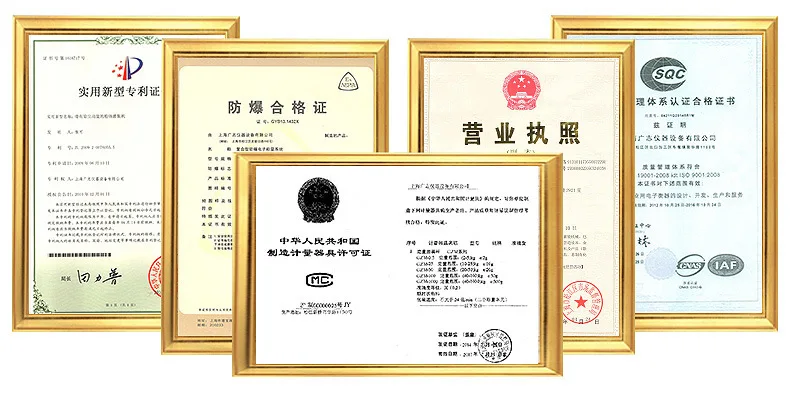
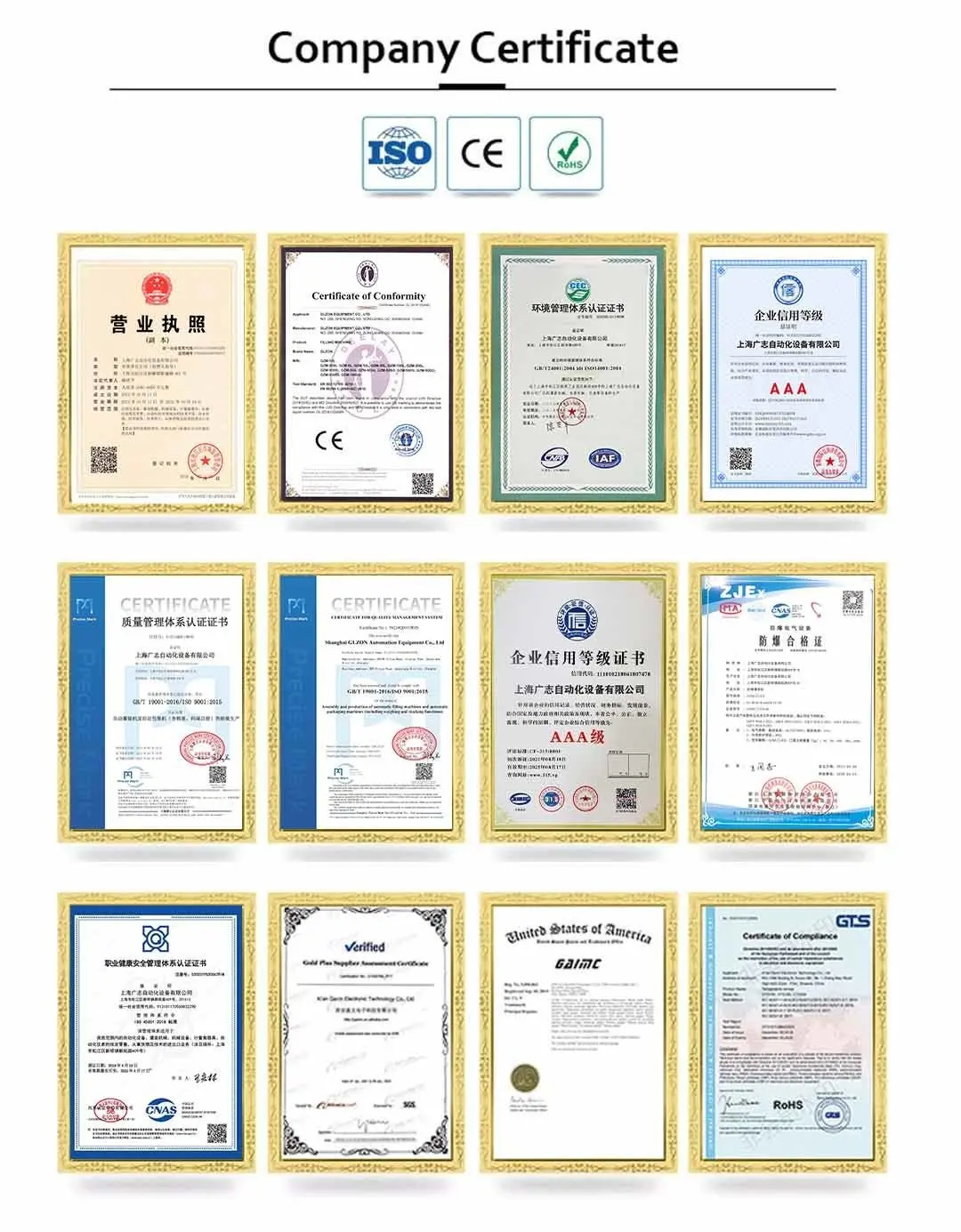
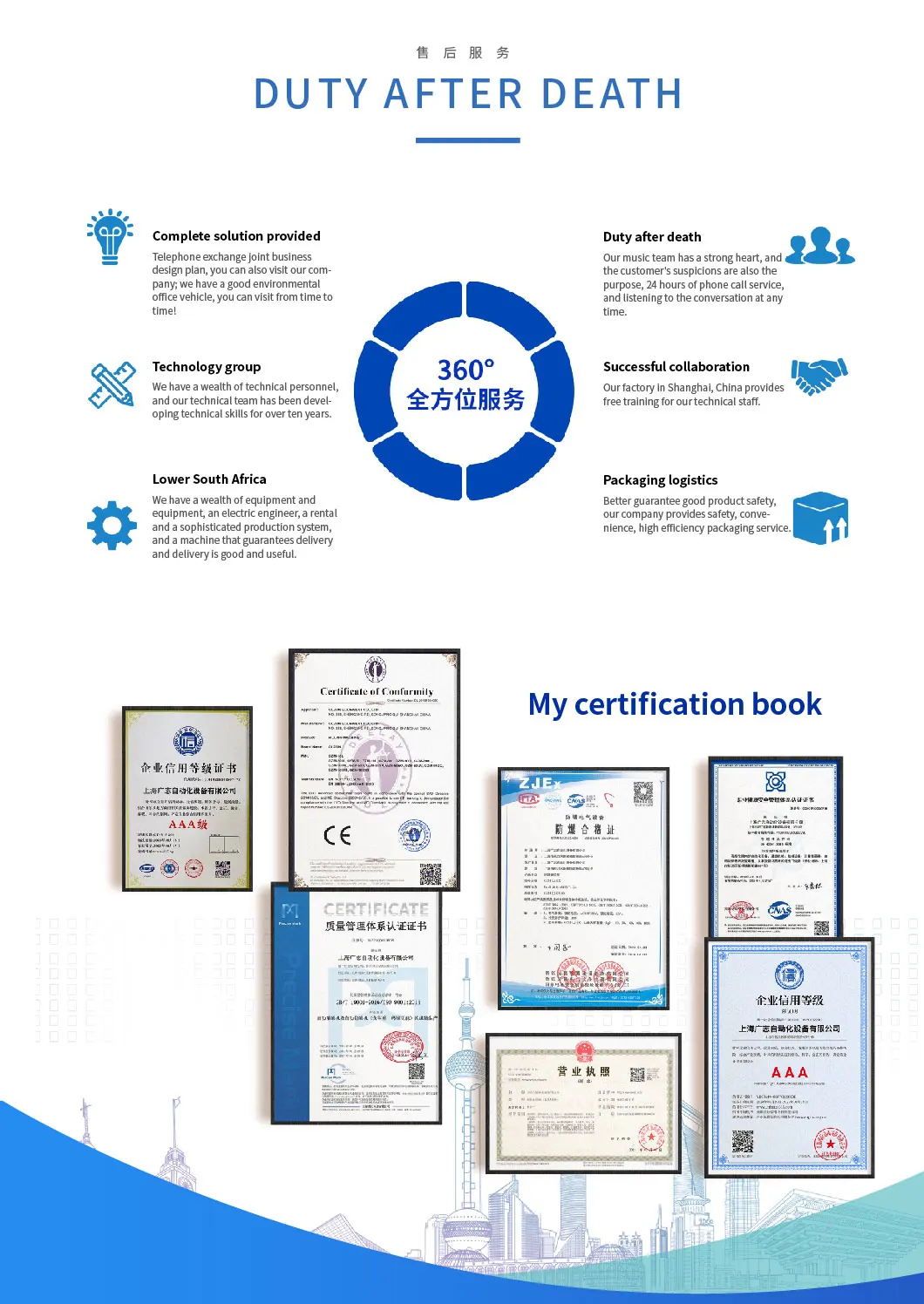
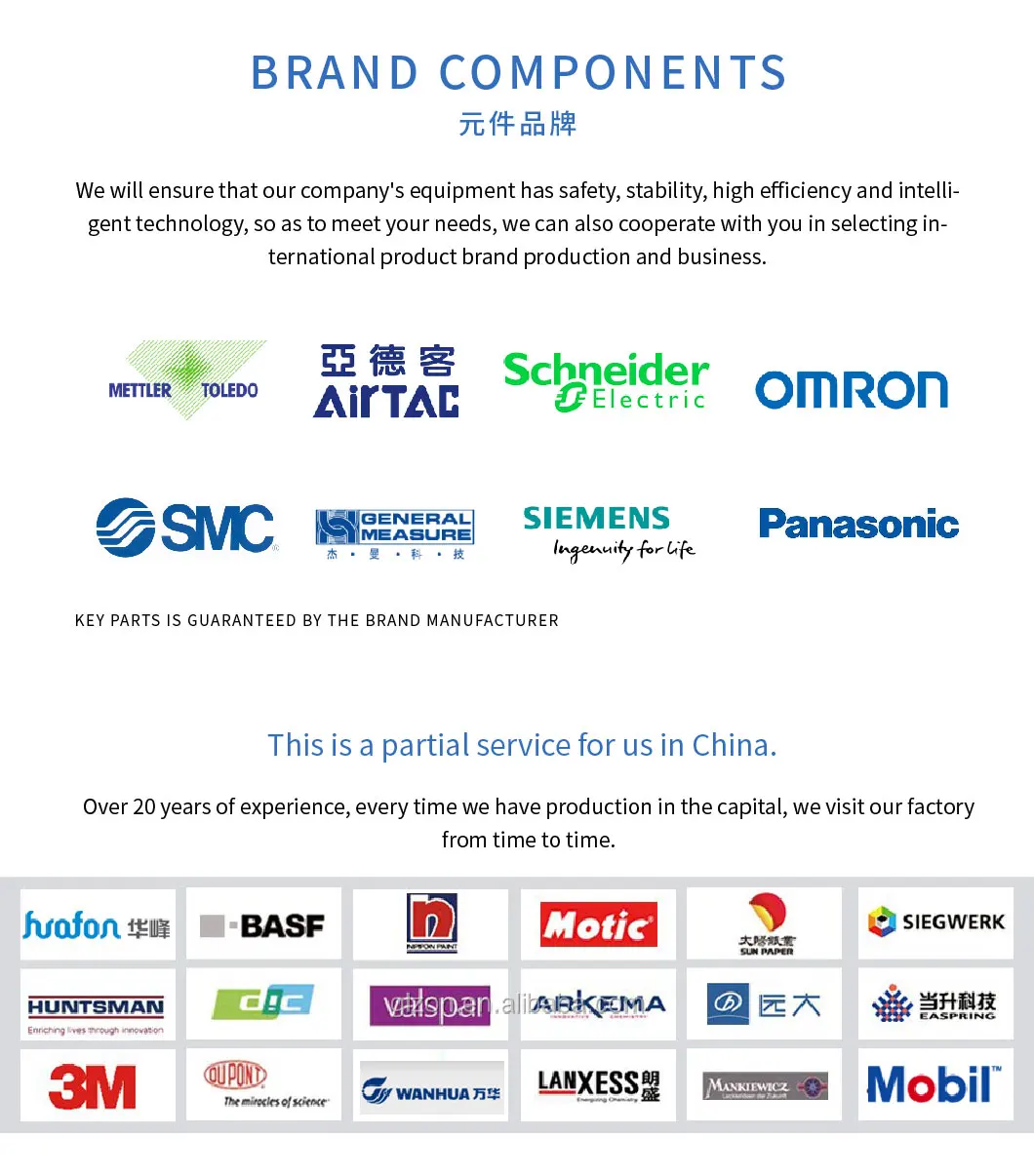
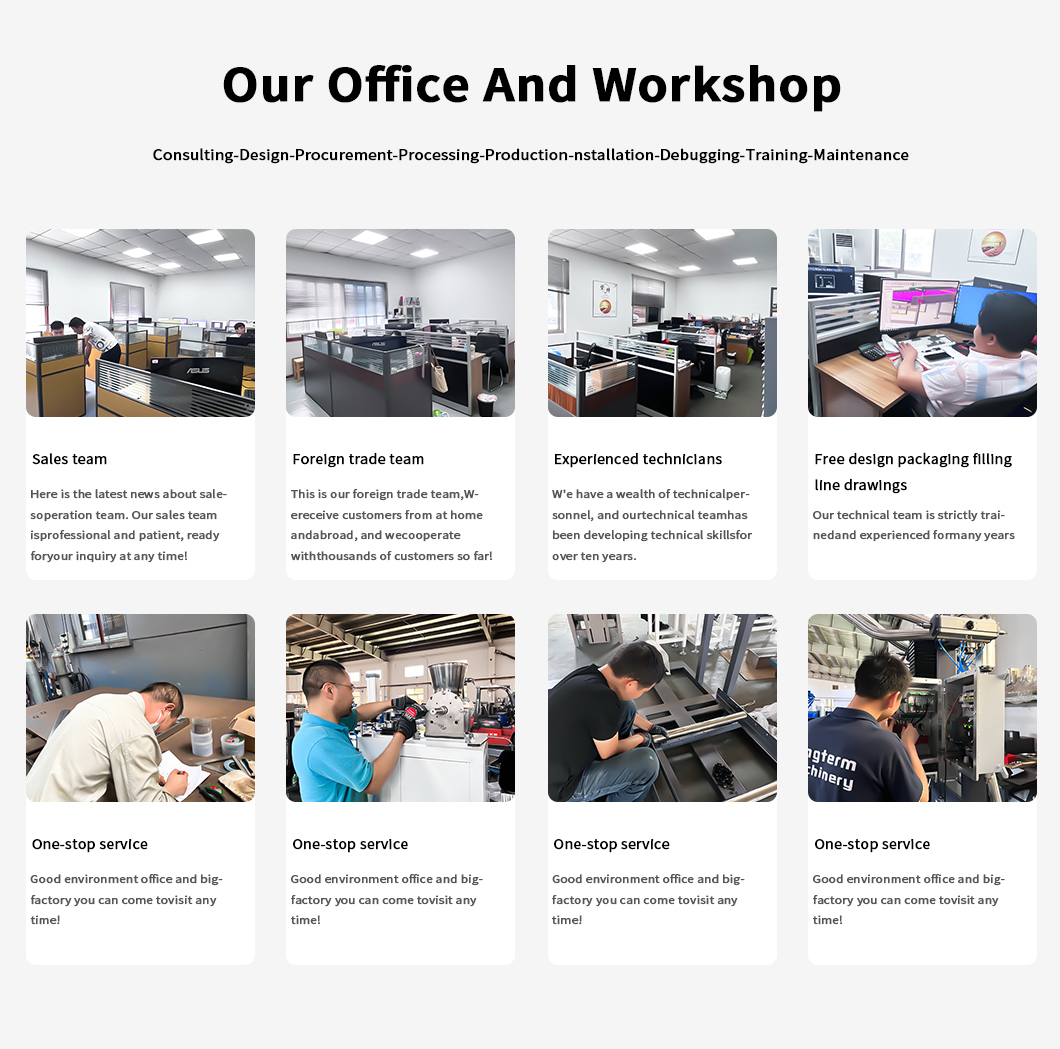
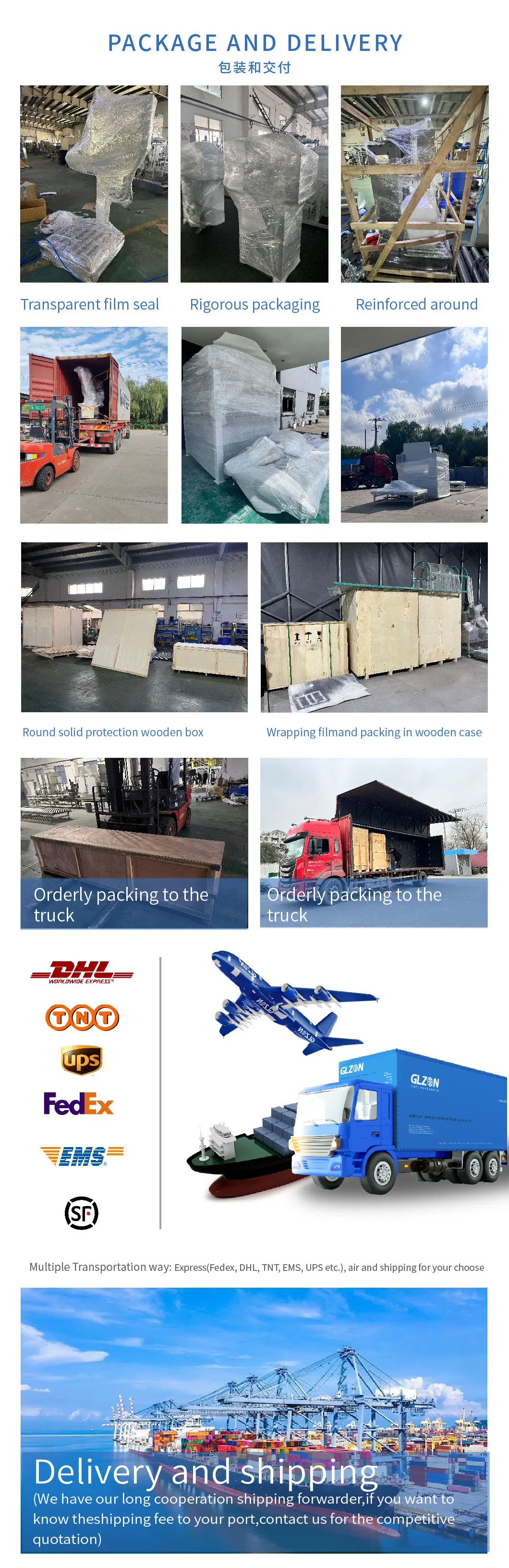